Pioniers schalen op in Plant One Rotterdam
Ook (internationale) multinationals vinden hun weg naar de Maasstad
Sinds de oprichting in 2015 heeft Plant One Rotterdam haar beloften meer dan waargemaakt. Bedrijven en onderzoeksinstellingen vinden hier alles wat nodig is om innovatieve ideeën op het vlak van duurzaamheid te ontwikkelen en op te schalen tot een commercieel proces of product. Hoe goed het concept werkt, blijkt uit de pioniers van het eerste uur die de fase van labonderzoek achter zich hebben liggen en hun ideeën opschalen of zelfs vermarkten. Het vliegwiel is in beweging.
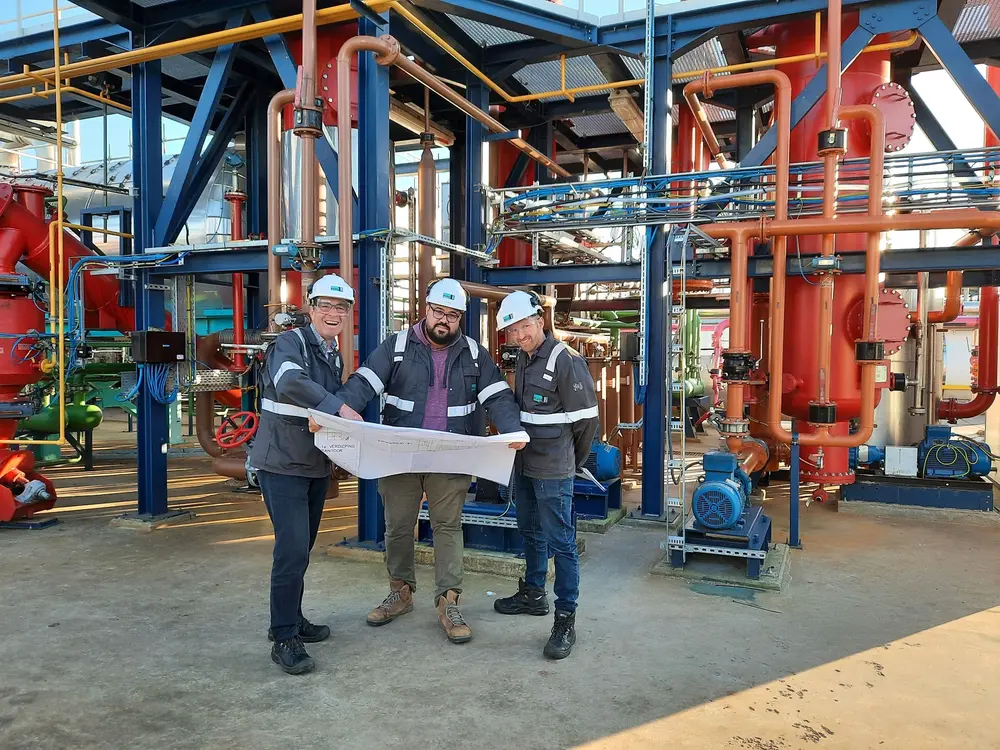
"Er zijn zoveel technologieën beschikbaar om de wereld duurzamer te maken. Die moeten zo snel mogelijk naar de markt!”
Voor wie het de afgelopen jaren heeft gemist: Plant One Rotterdam is een locatie op het Huntsman-terrein in de Rotterdamse haven waar iedereen met goede ideeën op het vlak van duurzaamheid in combinatie met chemische en procestechnologie, terecht kan om deze uit te werken tot een marktrijp product. Gabriël Tschin richtte hiermee een ‘gewoon’ commercieel bedrijf op dat haar eigen broek moet ophouden door haar klanten kwalitatief hoogwaardige diensten aan te bieden. Hiermee onderscheidt Plant One zich van overheidsgerelateerde innovatiecentra en particuliere, gesubsidieerde initiatieven.
Zo snel mogelijk naar de markt brengen
Fer Klinckhamers is sinds vorig jaar CCO bij deze BV en geeft aan: “Ons bestaansrecht hangt samen met de doelstelling om nieuwe technologie zo snel mogelijk beschikbaar te kunnen maken voor de markt om zo een steentje bij te dragen aan het verduurzamen van onze wereld. De noodzaak hiervan hoef ik denk ik niet uit te leggen. Maar dat is niet het enige. Om dit waar te maken, bieden we enkele unieke diensten met een belangrijke meerwaarde voor innovators.”
Klinckhamers doelt op de unieke milieuvergunning en de vele faciliteiten waarmee uiteenlopende testen veilig, verantwoord en wetconform zijn uit te voeren. “Daarnaast ondersteunen onze eigen mensen in de engineeringfase maar tevens bij de bouw, bediening en het onderhoud van een (proef)installatie. Een serieus onderscheidende factor. Niet zelden raken ideeën in de spreekwoordelijke lade omdat de betreffende innovator moeite heeft met het bouwen van een opstelling om zijn idee te testen en verder uit te werken tot opschaling mogelijk is. Onze ‘allrounders’ helpen op basis van een grote hoeveelheid kennis en ervaring. Zíj hebben de potentie om de kinderziektes – die nu eenmaal alle nieuwe installaties hebben – snel te achterhalen en op te lossen. Maar ook om deze draaiende te houden bij steeds weer bijgestelde procesparameters. Ook buiten de kantooruren.”
Internationale partners
Een unieke aanpak op een uniek terrein met gedreven mensen heeft ertoe geleid dat Plant One Rotterdam zich de afgelopen jaren serieus op de kaart heeft gezet. Dit is ook zichtbaar in de samenstelling van de groep klanten. Waar in het begin vooral start-ups hun weg vonden naar deze testfaciliteit voor innovatie in de procestechnologie, zijn inmiddels ook multinationals aangehaakt en is er tevens belangstelling getoond vanuit het buitenland.
Synthetische koolstof voor Li-ion batterijen
Eén van deze grotere bedrijven is Heraeus. Een familiebedrijf met wereldwijd bijna 15.000 medewerkers en een jaarlijkse omzet van ruim 30 miljard euro. Het concern omvat bedrijven in o.a. de sectoren elektronica, medische en industriële toepassingen. Menno Rus is sinds anderhalf jaar werkzaam als plant manager en gevraagd om een start-up op te zetten voor de ontwikkeling van een synthetische koolstof waarmee batterijen sneller kunnen laden en ontladen, een langere levensduur hebben en daarnaast minder warmte ontwikkelen. Onder meer belangrijk om het thema ‘e-mobility’ verder te concretiseren.
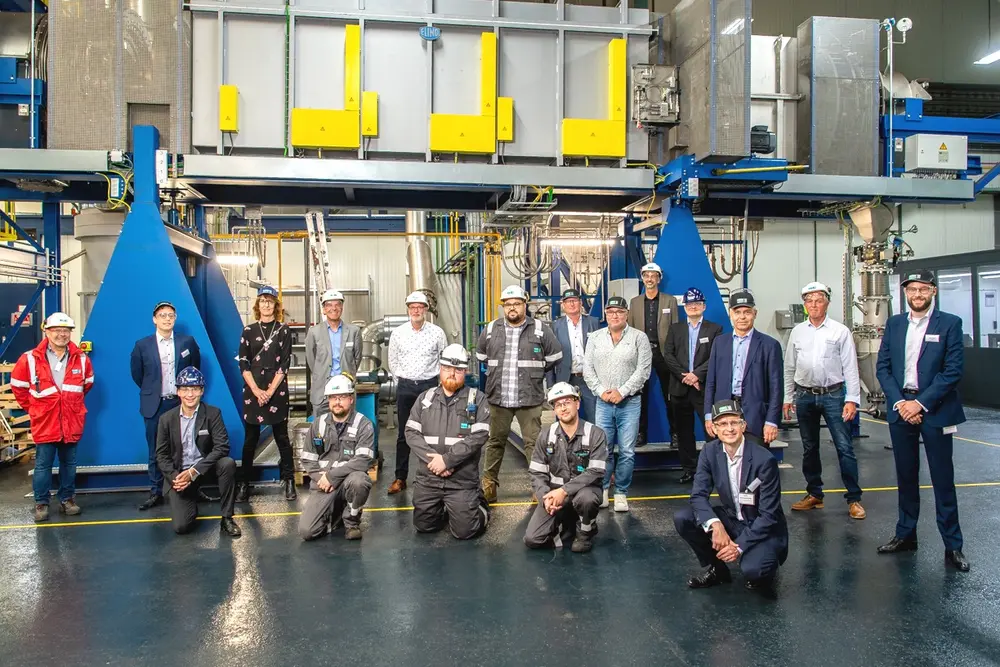
Rus: “Sinds 2008 zijn tientallen recepten getest en enkele generaties ontwikkeld. Met de kortgeleden ontwikkelde derde generatie hebben we een versie in handen die geschikt is voor grootschalige productie. Om deze opschalingsfase snel te kunnen doorlopen, is het noodzakelijk een proefopstelling te bouwen. Hiervoor hebben we Plant One Rotterdam benaderd. Zij hebben immers al de benodigde milieuvergunning en daarnaast hebben hun mensen een bijdrage geleverd aan de opbouw van de installatie die nu ook door hen wordt bediend. Bovendien zijn we erachter gekomen dat de regio Rotterdam binnen een straal van zo’n dertig kilometer over alle mogelijke serviceverlenende bedrijven beschikt. Ik kan hier letterlijk álles in de buurt vinden; ook wanneer het exotisch is.”
Opening
De officiële opening van de pilot plant was op 13 juli van dit jaar. De periode hieraan voorafgaand valt onder het hoofdstuk ‘uitdagend’. Menno Rus: “Bij het opbouwen van de pilot zaten we midden in de coronatijd. Redelijk onverwacht mochten medewerkers van een toeleverancier niet meer naar Nederland komen. Hierdoor hebben we de installatie zelf in bedrijf moeten stellen door middel van een smartphoneverbinding waarbij onze partner – puur directief – stap voor stap aangaf wat me moesten doen. Echt op het niveau: open die klep, draai die bout aan. Uitdagend en dynamisch maar we zijn begonnen!”
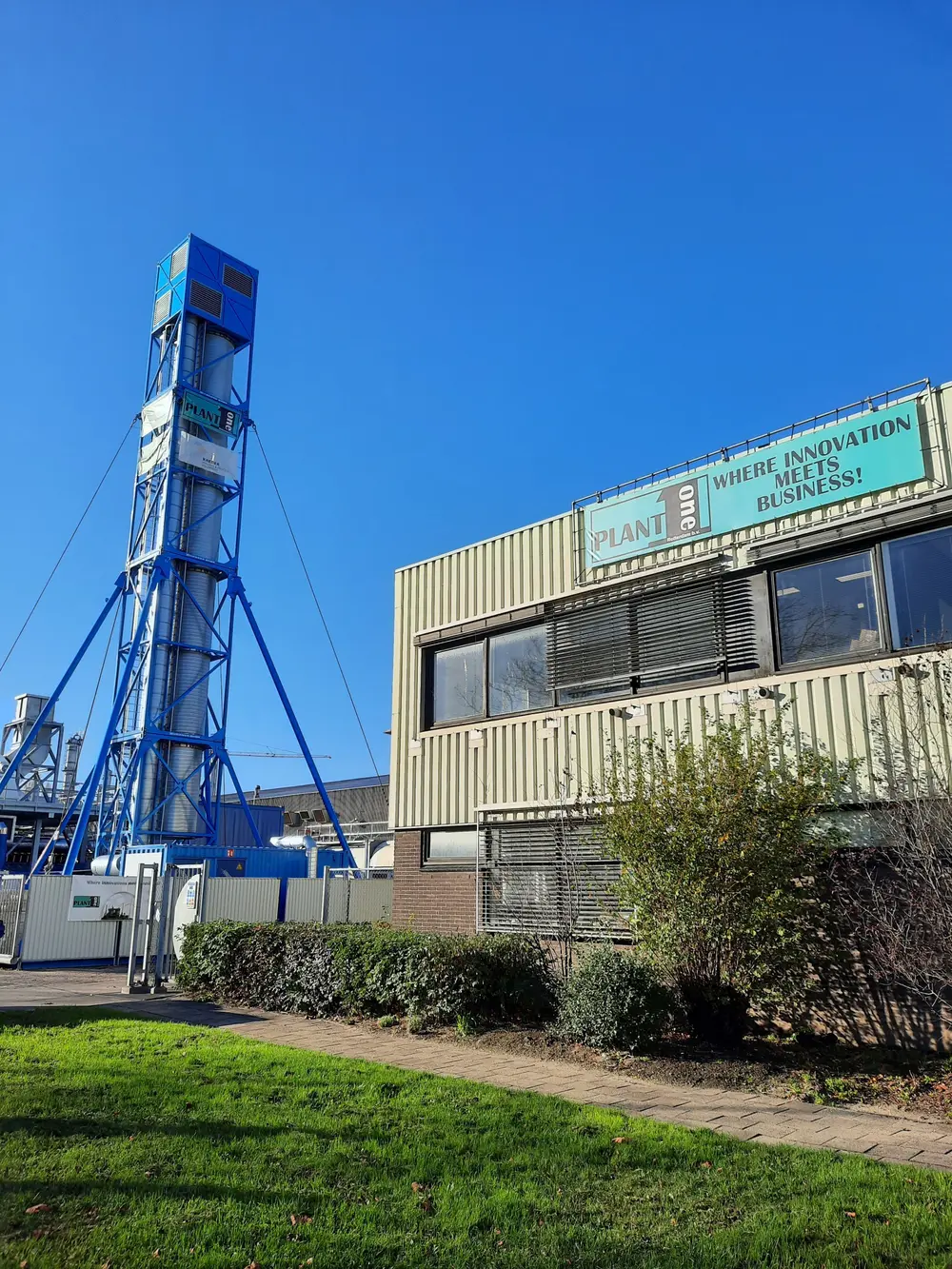
Jongeren betrekken
Het vliegwiel van Plant One Rotterdam dat met vereende krachten in beweging is gezet, drááit. Zowel de laboratoria als de hallen voor de pilotinstallaties worden goed gebruikt door een mengelmoes van wetenschappers, Willy Wortels en pragmatische technici. Dit allemaal in een informele sfeer die ook zo kenmerkend is voor het bedrijf. Fer Klinckhamers: “Enerzijds heb je te maken met geheimhouding, anderzijds heerst er een sfeer van vertrouwen en onderlinge behulpzaamheid die het werken hier meer dan prettig maakt.
Qua groei zijn we onder meer bezig met het uitbreiden van onze eigen disciplines om zo invulling te geven aan ‘ketenintegratie’ en circulariteit. Wat een afval- of restproduct is voor het ene bedrijf, kan fungeren als grondstof voor een ander. Hiervoor werken we samen met diverse opleidingsinstituten. Van de Hogeschool Rotterdam hebben we eigenlijk altijd stagiaires en afstudeerders binnen van wie er ook een aantal na het afronden van hun opleiding is blijven werken. Ook studenten van het Proces & Maintenance College zijn hier altijd te vinden. Wat aanspreekt, is de enorme diversiteit aan werkzaamheden en daarnaast de pragmatische aanpak die zo kenmerkend is voor Rotterdam. Met z’n allen de mouwen opstropen. Er zijn zoveel technologieën beschikbaar om de wereld duurzamer te maken. Die moeten naar de markt. En graag zo snel mogelijk.”
Plant-oner van het eerste uur
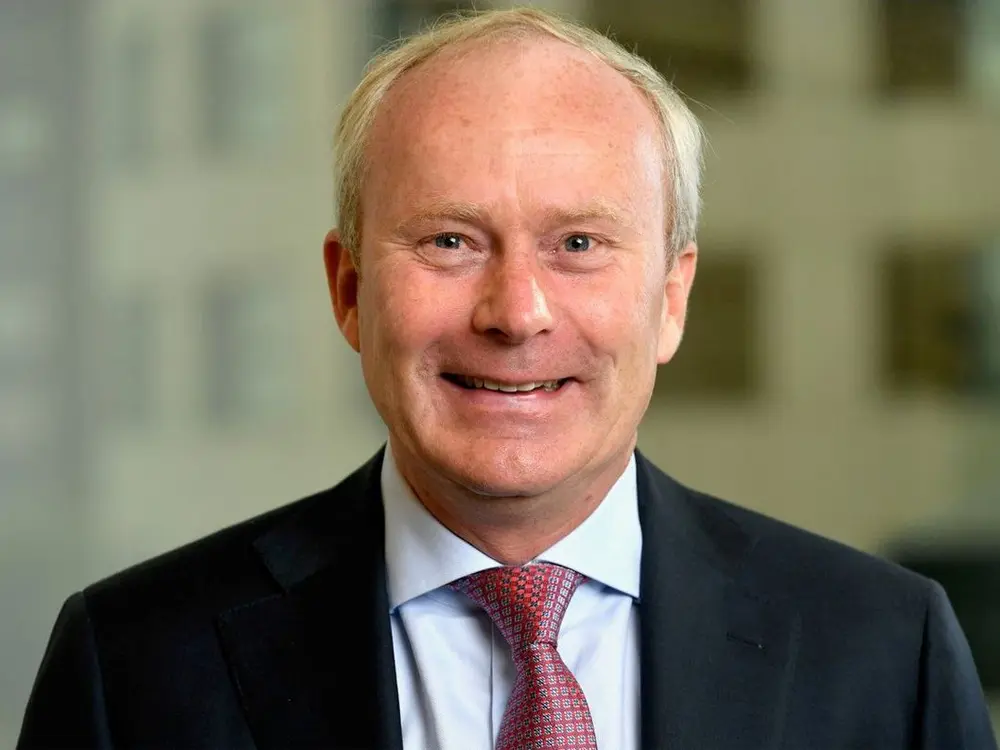
OBBOTEC is een van de bedrijven die zelf aan de wieg heeft gestaan van de oprichting van Plant One Rotterdam. De leiding ligt in handen van drie mannen. Onder hen de zoon van Obbo Hazewinkel. Een uitvinder in hart en nieren die zijn tijd ver vooruit was toen hij oplossingen bedacht voor de reductie van het gebruik van fossiele grondstoffen voor de productie van kunststoffen. Een tweede man is Wouter van Neerbos die 25 jaar ervaring heeft bij Shell en binnen dit bedrijf de algemeen directeur is met een commerciële en financieel economische achtergrond. Hij vertelt: “Obbo Hazewinkel had vele ideeën op de spreekwoordelijke plank liggen waarvan de rechten na zijn overlijden bij zijn kinderen terechtkwamen. Hieruit zijn de twee meest veelbelovende processen gekozen om verder te ontwikkelen: hydrocracking en selectieve plastic extractie.”
Hydrocracking
Het eerste betreft een hydropyrolyseproces waarbij een mix van bio-en pasticafval wordt omgezet in olie zoals scheepsvaartbrandstof. De combinatie is bewust gekozen omdat dit het hoofdbestanddeel is van bijna iedere huishoudelijke vuilnisemmer. Daarnaast produceren typisch land -en tuinbouwbedrijven dit afval. Wouter van Neerbos: “Lastig te verwerken omdat het om een mix van chemisch en organisch materiaal gaat en er weinig andere alternatieven waren dan verbranding.”
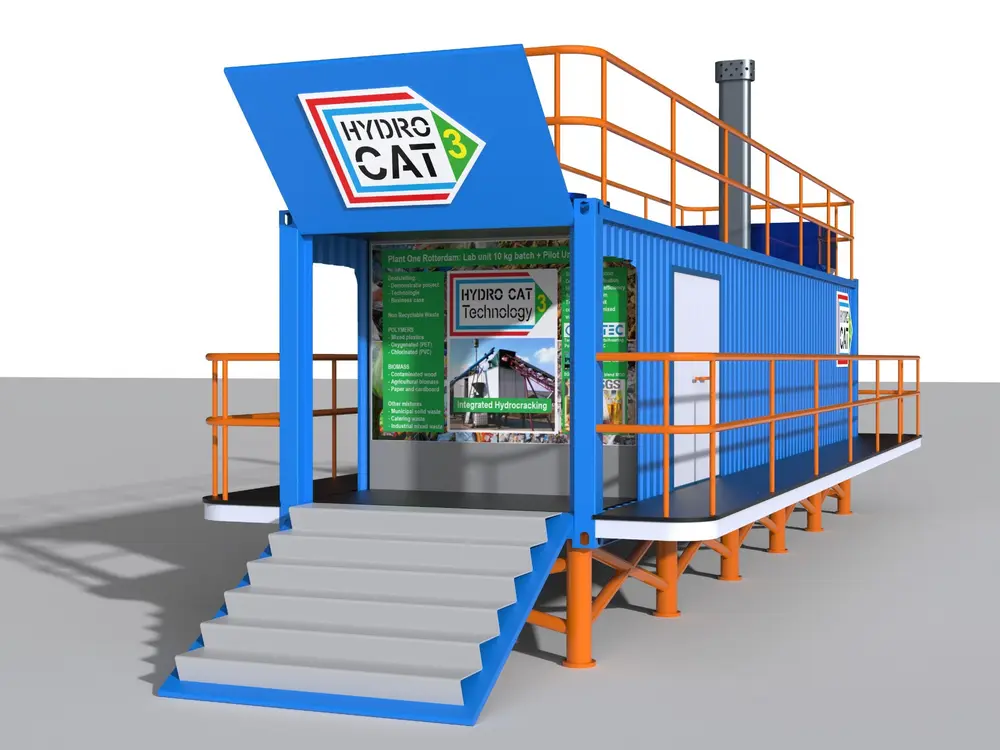
Door hydrocracking is de materiaalstroom echter op te waarderen naar olie, gas of nafta. Hiervoor wordt het eerst klein gemaakt in een shredder en daarna in de HydroCat-unit verwerkt inclusief een verrijking met waterstof. Binnen Plant One Rotterdam wil OBBOTEC opschalen naar een unit van tien kiloton per jaar. Hun businessmodel is gebaseerd op kleinere decentrale oplossingen die bijvoorbeeld worden geplaatst of gemeenteterreinen, bij bedrijven als KLM of afgelegen gebieden zoals de Waddeneilanden.
Met SPEX worden de polymeren opgelost en gezuiverd middels verschillende filtratie- en wasprocessen
Selectieve Plastic EXtractie
Het tweede proces waarvoor binnen Plant One Rotterdam een pilot wordt gebouwd, is Selectieve Plastic EXtractie. Kortweg SPEX. Een proces waarmee van vervuild polyethyleen (PE) en polypropyleen (PP) ‘near-virgin’ granulaat is te maken. Bij vervuiling valt te denken aan additieven als kleur- en geurstoffen, weekmakers of brandvertragers.
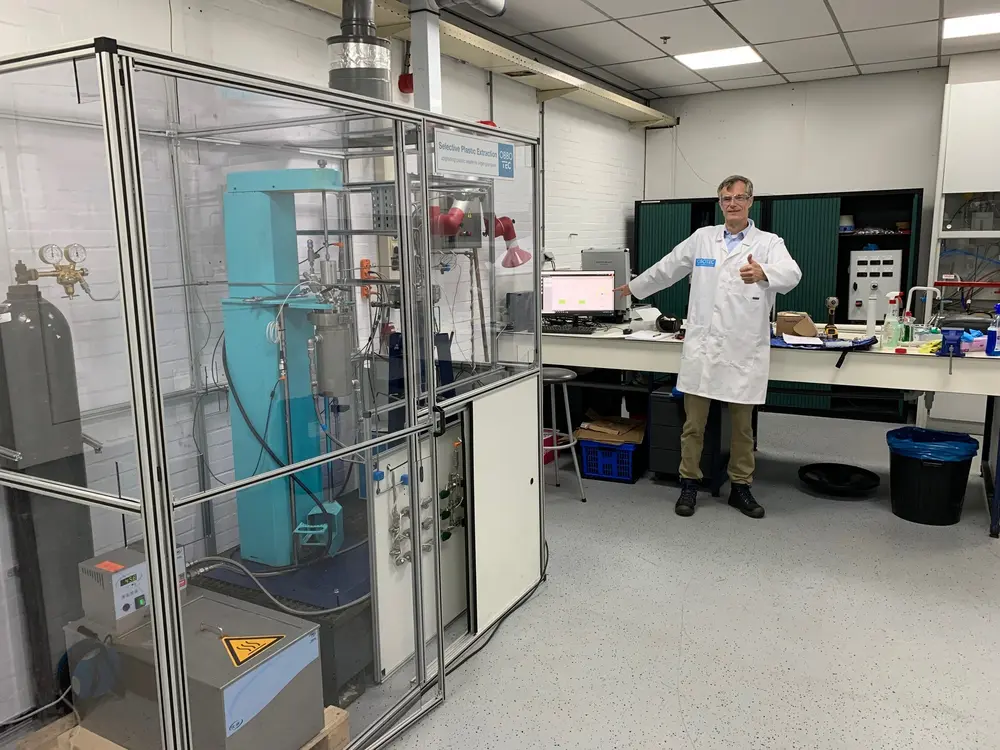
Met SPEX worden de polymeren opgelost en gezuiverd middels verschillende filtratie- en wasprocessen. Wouter van Neerbos: “Met deze techniek zitten we een beetje tussen chemisch en mechanisch recyclen in. Bij mechanisch recyclen heb je het voordeel dat je de volledige materiaalstroom hergebruikt maar het nadeel is dat alle additieven aanwezig blijven. Bij chemische recycling breek je plastic af tot oorspronkelijke bouwstenen. Hiermee ben je de additieven kwijt maar ook de samenstelling van je polymeren. Dit afbreken en daarna weer opbouwen naar kunststof heeft een impact op de yield en kost bovendien relatief veel energie. Met SPEX behoud je de voordelen van beide technieken: enerzijds een hoge yield van rond de 95% en anderzijds het behoud van je oorspronkelijke polymeren.”
Voor beide processen zijn binnen Plant One Rotterdam inmiddels pilot installaties gebouwd waarmee de weg is ingeslagen richting opschaling voor commerciële toepassingen. “We hebben hier echt de one-stop-shop gevonden die we nodig hebben”, weet Van Neerbos. “Alle vergunningen zijn hier geregeld en we kunnen gebruikmaken van alle utiliteiten, equipment en mensen die ons ondersteunen bij zowel het ontwerp als de proefopstelling. Bovendien pakken mensen hier dóór; zonder concessies te doen aan de kwaliteit.”