DES FORMES CINTREES NATURELLES REHAUSSENT LE CACHET DU PARQUET
CONCEPT DE PRODUCTION UNIQUE POUR UN PRODUIT FINI DE HAUTE VALEUR
Le producteur hollandais de parquets Bolefloor fait fureur actuellement avec un parquet dont les parties ne sont pas droites mais adoptent des courbures naturelles. A la base de ce produit unique réside un processus de production élaboré qui fait co-habiter un scanner intelligent, un logiciel CAO/FAO spécialement fait sur mesure et une technique CNC ultra moderne. Comme placeur, vous devez accorder une grande attention au mesurage correct. Une exécution minutieuse est également importante étant donné que chaque planche est unique.
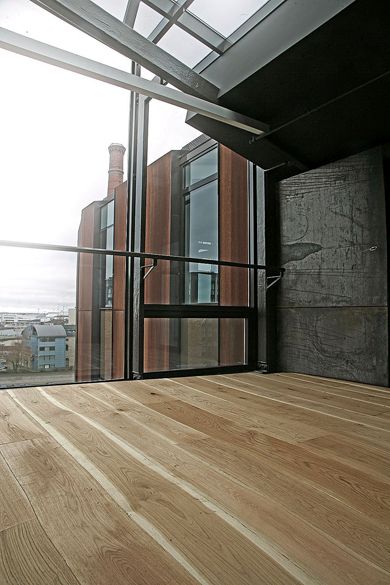
AMBIANCE RUSTIQUE ET ASPECT NATUREL
L'idée de la production de parties de plancher cintrées n'est pas flambant neuve. Depuis des années, il existe une demande de parquet avec des raccords naturellement ondulés. Ils sont surtout prisés pour l'ambiance rustique qu'ils évoquent et sont fréquents dans les châteaux et les propriétés luxueuses.
Seuls quelques artisans expérimentés et très passionnés étaient capables de créer de tels sols en bois. Leur rare compétence technique et les nombreuses heures consacrées à la production et au placement ont fait que le parquet aux formes bombées était quasi impayable.
Aujourd'hui, la technologie ultra moderne permet toutefois de produire automatiquement les parties de plancher cintrées, et donc à des prix plus démocratiques. Le concepteur et précurseur de ce concept est Bolefloor, une entreprise hollandaise avec un établissement de production en Estonie. Dans ce qui suit, vous saurez tout de la méthode de travail.
RABOTER ET SCANNER
Un premier composant au sein du processus de production élaboré est un système de scanning intelligent, mis au point par la société finlandaise Delta-Enterprise. Les planches sciées entrent dans l'usine fortement séchées et en plots et sont acheminées par un convoyeur à bande à travers une dégauchisseuse et un scanner. Le scanner dispose de deux caméras qui analysent en détails le dessus et le dessous de la planche. Ceci implique: déterminer les dimensions et contours, identifier l'aubier inutilisable et donc en même temps les parties utiles de la planche, détecter les noeuds et autres irrégularités dans la surface du bois, ainsi que filmer avec précision les nuances de couleur et la structure surfacique.
La résolution d'analyse de la planche est réellement stupéfiante: le scanner prend une image tous les demi-millimètres! Après le scanning, la partie utile est sciée automatiquement de la planche et reçoit un numéro d'identification unique avec une étiquette à codes barres pour disparaître finalement dans le stockage intermédiaire.
BANQUE DE DONNEES ET PROGRAMME CAO
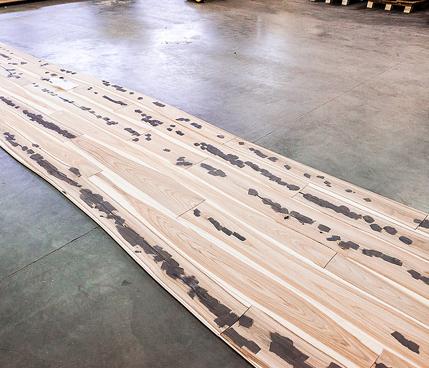
De cette manière, on dispose d'un dessin 3D détaillé de chaque planche présente dans le magasin. Celui-ci est sauvegardé dans une banque de données numérique qui fait office de source pour le programme CAO MicroStation Powerdraft. Ce programme de dessin est semi-automatique. Le concepteur réalise avant tout une représentation de l'espace sur base des dimensions transmises par l'architecte ou le placeur. Ensuite, il ajuste certains paramètres souhaités, comme l'essence, la largeur maximale ou minimale, la qualité du bois, la tolérance quant aux écarts de couleur ou de structure ...
Puis la conception du plancher effectif peut commencer. Après la sélection et la pose de la première planche, le programme CAD montre une série de planches qui correspondent étroitement à la planche déjà posée en termes de forme, de dimensions, de contours, de couleur ..... Ceci se fait à l'aide de puissants algorithmes d'optimisation. Au concepteur de sélectionner et positionner à chaque fois la planche suivante souhaitée. Ceci se poursuit jusqu'à ce que le plancher complet est conçu dans le programme CAO.
Naturellement, il est impossible de trouver à chaque fois une planche qui correspond à 100 %. De plus, le concepteur doit tenir compte du fait que la planche doit être pourvue d'une rainure et/ou une languette. Ceci signifie qu'il faut retrancher une certaine largeur minimale de chaque planche. Tout ceci est peaufiné dans le programme CAO.
POST-PROCESSEUR ET LIEN AVEC FAO
Maintenant que le projet est entièrement dessiné dans le programme CAO, on sait quelles planches seront utilisées et quelles forme d'ajustement précise elles doivent avoir. En partant de ces données, le post-processeur Woodwop génère les codes G pour le centre d'usinage qui réalisera les parties du plancher exactement sur mesure. Grâce à ce lien automatique entre CAO et FAO, il est possible de réaliser en seulement trois minutes les programmes de commande pour une centaine de planches de parquet différentes et uniques.
CENTRE D'USINAGE HOMAG
Les planches concernées sont ensuite retirées du magasin et placées une par une sur le centre d'usinage, un Homag Profi BOF211 ayant une plage de travail maximale de 7.300 mm x 1.550 mm. La table dispose de douze consoles avec à chaque fois quatre positions pour l'application des cups sous vide. En outre, les consoles sont commandées de façon entièrement automatique de manière à perdre le moins de temps possible dans le positionnement et le serrage des planches. Cette automatisation est possible du fait que les dimensions et les trajets de fraisage précis de chaque planche sont connus au préalable.
Les usinages proprement dits comprennent le fraisage sur mesure des planches et le fraisage de la rainure ou languette. En fonction du type d'usinage et du matériau (massif ou semi-massif, voir plus loin), l'outil de coupe adéquat doit être utilisé. L'outil est entraîné par une puissante broche principale quatre axes (14 kW). Le changement entre les outils est automatique: la broche peut interagir de façon totalement autonome avec le magasin à chaîne qui contient trente positions d'outil. Outre la broche principale, la machine dispose d'une unité de tête de perçage avec treize broches pour des usinages supplémentaires en dehors du champ d'application 'parquet', par exemple pour l'utilisation des planches comme revêtement mural, plateau de table ou plan de travail.
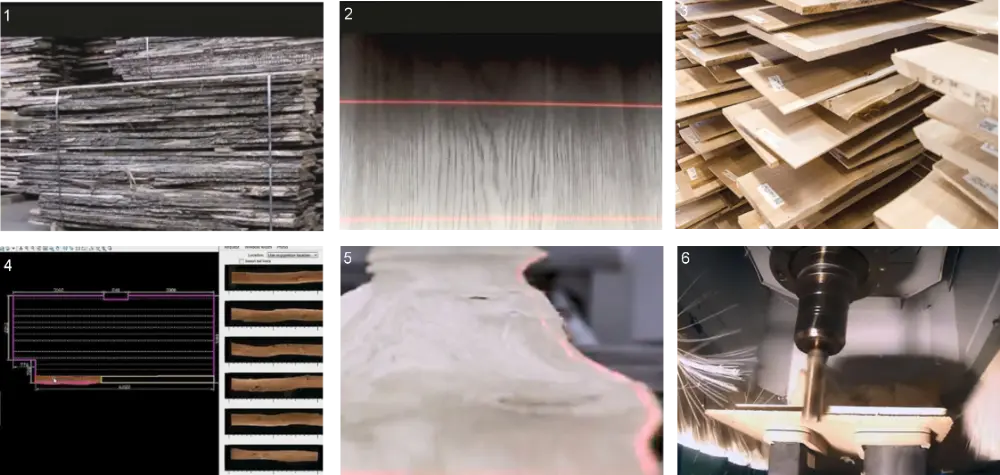
PONCER ET EMBALLER
Après l'usinage sur la défonceuse CNC quatre axes, les planches sont évidemment poncées à fond. Pour terminer, elles sont emballées. Cela ne se fait évidemment pas au petit bonheur mais par projet, ce qui souligne une fois encore qu'il ne s'agit pas ici de production de masse mais de travail industriel sur mesure. Chaque planche qui entre dans l'usine est en effet traitée comme un objet individuel et unique.
“LE MESURAGE DOIT CORRESPONDRE AU MILLIMETRE PRES”
Joris Van Ermen, gérant d'EXID bvba, est l'un des rares en Belgique à jouir de l'expérience du placement d'un Bolefloor: “Nous sommes une entreprise générale et de construction d'intérieurs établie à Bonheiden, fondée en 2006 et très active dans le monde de la rénovation et de la démolition. Notre terrain d'action se situe dans différents secteurs: particuliers, projets publics, horeca, retail, business ... J'ai découvert les planchers de Bolefloor via le site internet de médias sociaux 'pinterest'. Le produit nous semblait tout à fait adéquat pour notre client apotheek SALVIA à Keerbergen.
Le maître d'ouvrage, Catherine De Preter, cherchait un concept distinct avec uniquement des finitions qui ressortent réellement. Bolefoor était parfaitement en concordance. La finalisation concrète du projet a été rapide. Lors du mesurage, il est très important de respecter une grande précision. Le placement ne peut se faire que par des professionnels mais s'effectue via le système classique de la pose de parquet.”
VARIANTES
Essences
Le parquet peut être livré dans cinq essences: chêne, frêne, érable, noyer et cerisier.
Parquet massif ou composé
Hormis la production du parquet massif, il existe une variante en parquet composé (semi-massif) pour les environnements exigeants comme les locaux humides ou pour pouvoir combiner le parquet avec le chauffage par le sol. Naturellement, le processus de production du parquet composé est un peu plus fastidieux. Avant de le transformer sur mesure et de le profiler dans son ensemble sur la machine CNC, on doit en effet commencer par la transformation sur mesure du support multiplex et l'encollage du bois massif par-dessus. De plus, l'usinage sur la défonceuse CNC est un peu plus complexe.
Exécution rainurée ou non rainurée
Le choix porte également sur un parquet avec des raccords rainurés ou non rainurés (c'est-à-dire légèrement biseautés). Ceci est non seulement possible sur les longs côtés mais aussi sur les chants en bout.
CARACTERE VERT
Bolefloor souligne volontiers le caractère vert de son produit. En respectant autant que possible les formes cintrées naturelles du bois utile provenant des planches, on évite, dit-on, quelque 20 % de perte de matériau par rapport à la production de parties de parquet droites traditionnelles. De plus, le parquet fini confère aussi une ambiance naturelle et écologique à la pièce dans laquelle il est placé. Les chaînes de magasins, surtout, s'en rendent compte et déboursent volontiers davantage pour cela, parce qu'elles savent qu'en plus d'avoir un plancher unique, elles se voient affublées d'une image plus écologique.
BUDGET
Nul besoin de démontrer que le client final paie davantage pour un tel plancher que pour un plancher classique. Le prix indicatif moyen pour le plancher en soi oscille autour de € 125/m². Il faut encore y ajouter le coût du placement.
PLACEMENT
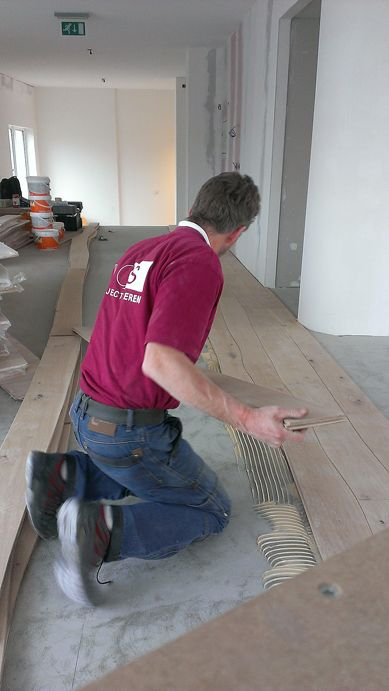
Bolefloor collabore avec des partenaires privilégiés mais livre également sur demande à d'autres professionnels.Ce qui est surtout important pour le placeur, c'est le mesurage. Celui-ci doit être extrêmement correct et précis, vu que chaque planche du plancher est déjà conçue à l'avance. Après la production de toutes ces parties de plancher séparées et uniques, il est donc assez difficile d'encore corriger si le mesurage proprement dit semble différer de quelques centimètres des dimensions réelles. Les professionnels qui ne sont pas sûrs de leur travail et ne veulent prendre aucun risque peuvent aussi faire appel à une équipe de mesurage de Bolefloor.
Dès que les parties de plancher sont produites, elles sont livrées dans un emballage individuel. Chaque planche est numérotée et à l'aide du plan du plancher fourni, le placeur peut aisément poser le parquet. Le mieux est de le faire de la façon classique, via l'encollage sur un sous-plancher adéquat. De plus, les parties de plancher s'encliquètent via l'assemblage à rainure et languette. Mais attention aux dommages: si une partie du plancher est irrémédiablement endommagée, elle doit être à nouveau produite entièrement sur mesure. Naturellement, ceci entraîne un coût supplémentaire et un délai de livraison.
AUTRES APPLICATIONS
Bien que le parquet soit l'utilisation la plus connue de ce produit, il peut aussi s'utiliser pour d'autres applications. Nous songeons aux meubles (p.e. panneaux de table ou de travail), panneaux de porte, revêtement mural ... Une version en placage spéciale a été conçue à cette fin.
Merci à Henri Vos (Bolefloor)