Converting biogas in clean hydrogen
bionico: Biogas membrane reformer for decentralized hydrogen production
The recently finalized BIONICO project was granted by the European commission through the Hydrogen and Fuel cell joint undertaking initiative. BIONICO stands for “Biogas membrane reformer for decentralized hydrogen production”. The main objective of BIONICO was to build and demonstrate in an existing biogas plant pure hydrogen production by direct biogas conversion through a novel membrane reformer. The hydrogen production capacity selected for the project was approximately 100 kg/day of pure hydrogen. Prof. Fausto Gallucci discusses the results and challenges of the BIONICO project, where he acted as Technical Manager of the complete project.
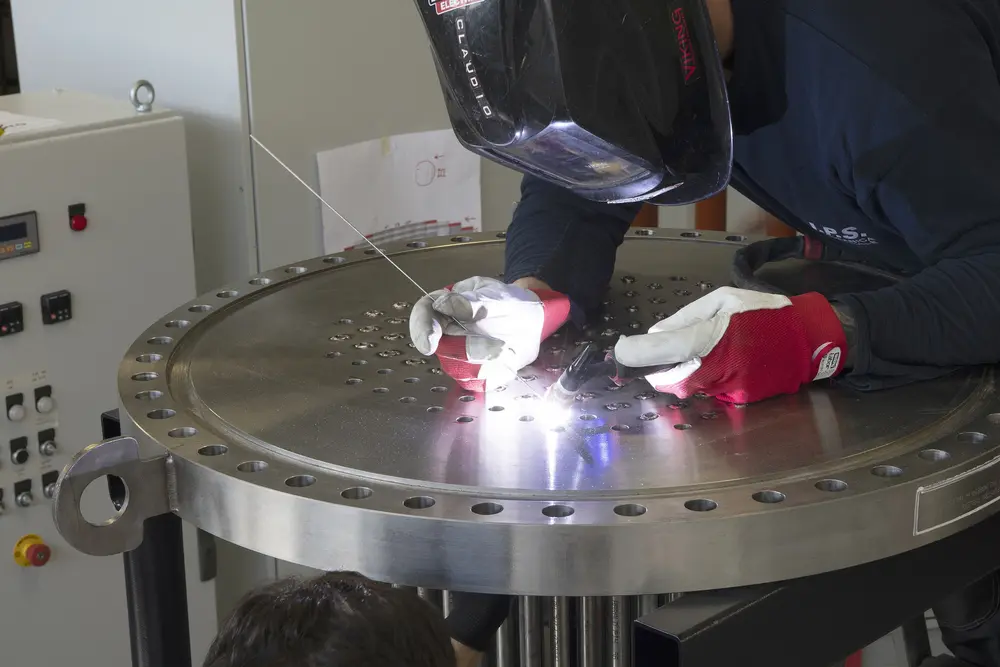
The project partners were able to produce and integrate a very large amount of membranes
novel intensified reactor
BIONICO consortium has been able to develop, build and demonstrate in industrially relevant environment (TRL6) a novel reactor concept integrating H2 production and separation in a single vessel.
By using the novel intensified reactor, direct conversion of biogas to pure hydrogen is achieved in a single step, which results in an increase of the overall efficiency and strong decrease of volumes and auxiliary heat management units.
In particular, by integrating the separation of hydrogen in situ during the reforming reaction, the methane in the biogas will be converted to hydrogen at a much lower temperature (550 °C) compared with a conventional reforming system (850-950 °C), due to the shifting effect on the equilibrium conversion. The fluidization of the catalyst makes also possible to (i) overcome problems with temperature control (formation of hotspots or too low temperature), (ii) to operate with smaller particles while still maintaining very low pressure drops and (iii) to overcome any concentration polarization issue associated with more conventional fixed bed membrane reactors. A schematic picture of the reactor is reported in Figure 1 (for simplicity the catalyst is not shown in the picture).
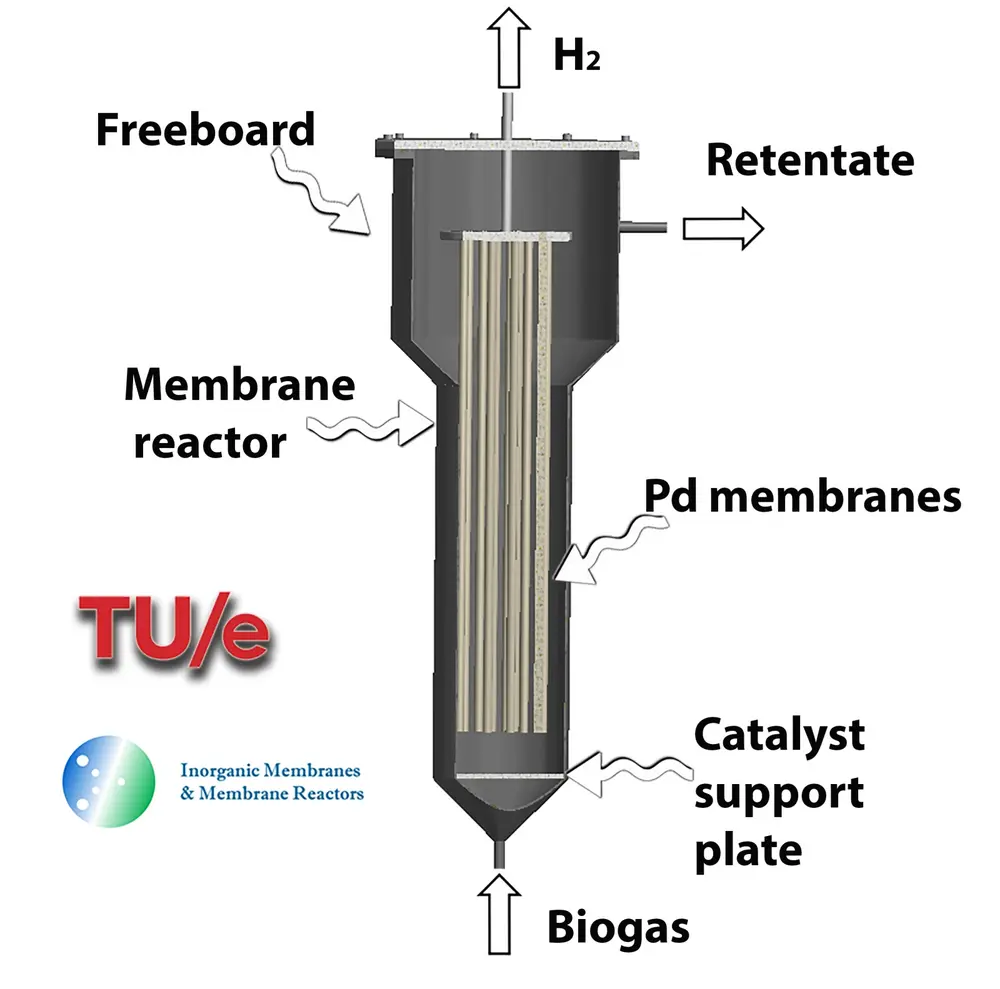
stronger membranes
The core of the process is obviously the combination of the reaction with the membrane separation for hydrogen recovery. One of the main objectives of the project was to develop stronger thin layer palladium based membranes that could be more easily integrated in fluidized bed reactors and could be produced in larger quantities.
For this, new supports have been developed that are stronger, have a finger-like configuration and are produced at semi-industrial scale. The quality of the support is such that thin palladium layers can be deposited without any other pre-treatment.
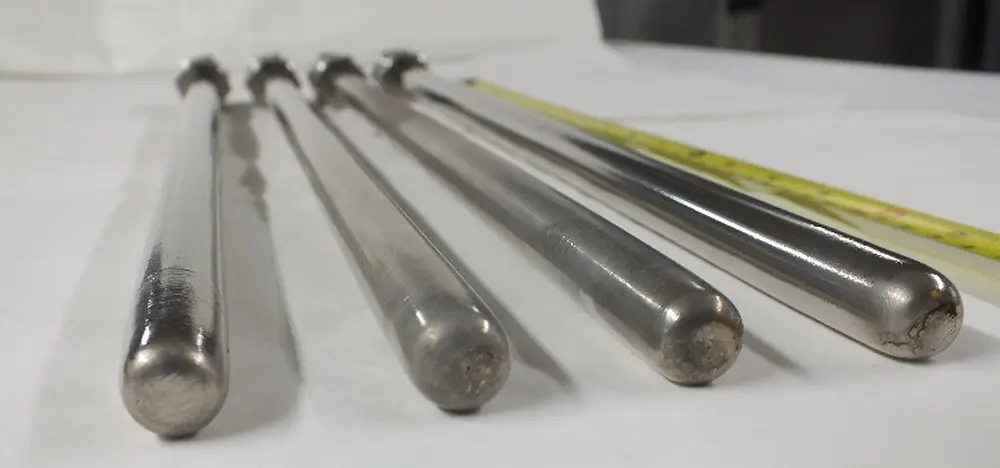
We have been working on both the membrane preparation and membrane evaluation. We have shown that the new configuration is more stable than previous membranes even under fluidization conditions, and the leak rate (which influence the hydrogen purity) is half the one of standard open-end membranes. So that we expect half impurities in the hydrogen produced. The BIONICO project also developed quality control procedures for both supports and membranes. And, with detailed experiments and modelling, the best membrane integration has been designed.
The project partners were able to produce and integrate a very large amount of membranes, making the BIONICO reactor the reactor with the largest membrane area installed so far.
The BIONICO reactor has the largest membrane area installed so far
Why fluidized bed membrane reactor?
The application of membrane reactors for the selective recovery of hydrogen during the hydrogen production has been extensively studied over the years. Different membrane reactor designs have been proposed and these include, packed bed membrane reactors, fluidized bed membrane reactors and microchannel membrane reactors.
For reactions like steam reforming of methane or autothermal reforming of natural gas (as for the BIONICO project) there are two important criteria to be considered when selecting the reactor configuration. Firstly, these reactions are highly endothermic (steam reforming) or combine highly endothermic and highly exothermic reactions (like for BIONICO). To avoid damaging the membranes, the heat management (i.e. good heat transfer rate) is very important.
Secondly, we are now able to produce very thin membranes with high fluxes, which require reactor concepts that allow much higher mass transfer rate.
The combination of these requirements together with the relatively large amount of flows to be treated, drove our selection for the fluidized bed membrane reactor configuration.
In the fluidized bed membrane reactor, the membranes are immersed in bed of catalytic particles. The catalytic particles are brought to fluid like conditions where the superficial gas flow counter balances the frictional forces of the catalytic parties. A bubbling behavior of the bed is achieved with a high enough gas velocity. While the particles are moving inside the reactor, they allow high heat transfer and mass transfer rates. Additionally, for an optimal design of the reactor, the particles are relatively small (below 0.2 mm) and this also allows us to avoid intraparticle mass transfer limitations.
On the other hand, moving particles also result in attrition inside the reactor. As such we have developed new membranes that are more stable in fluidized bed conditions and new catalysts especially designed for fluidized bed membrane reactors.
first plant of this size
Finally, with ICI Caldaie (Italy) as system integrator, the final plant has been installed and tested for a few hr, in Italy.
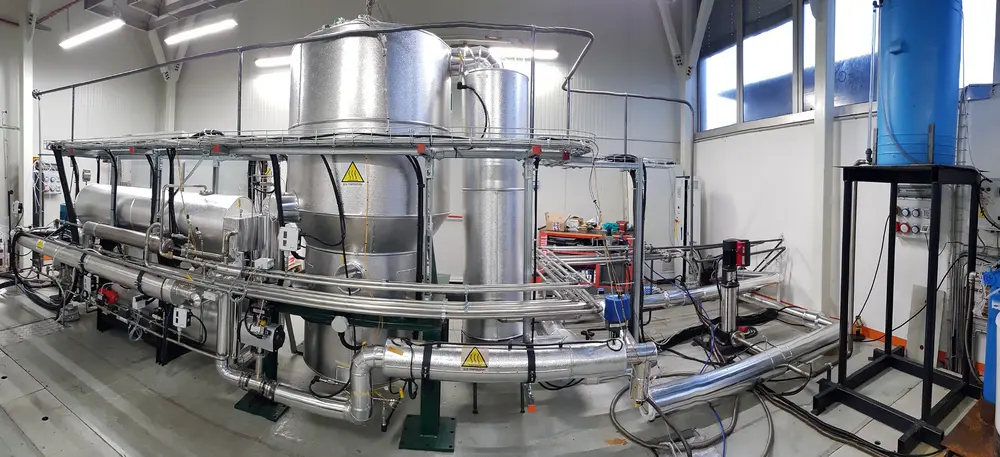
This is the first time a membrane reactor plant of this size for biogas treatment has been realized within a EU project. While we have been able to demonstrate the scale-up of the membrane production and membrane reactors to a much larger scale than previously shown, we have also encountered quite a large amount of challenges. Most notably, the process industry is not yet ready for small scale distributed production. Most of the components do not exist at this scale, which makes the construction of the system very time consuming and expensive. Nonetheless, apart the technical challenges, has been demonstrated that the membrane reactor concept is applicable for production of industrial gases, and in particular hydrogen for fuel cell applications.
The process industry is not yet ready for small scale distributed production
This concept is now further developed in the MACBETH project, where membrane reactors are being constructed and tested for a cumulative time of 35000 hr in industrial environment, before entering in commercialization.
For the commercialization, Eindhoven University of Technology, together with Tecnalia Research (Spain), with the support of ENGIE (France) have now created a company called H2SITE, for the industrial production of membranes and integration of membrane reactors for pure hydrogen production. The first commercial units are being validated and certified before entering into the market.
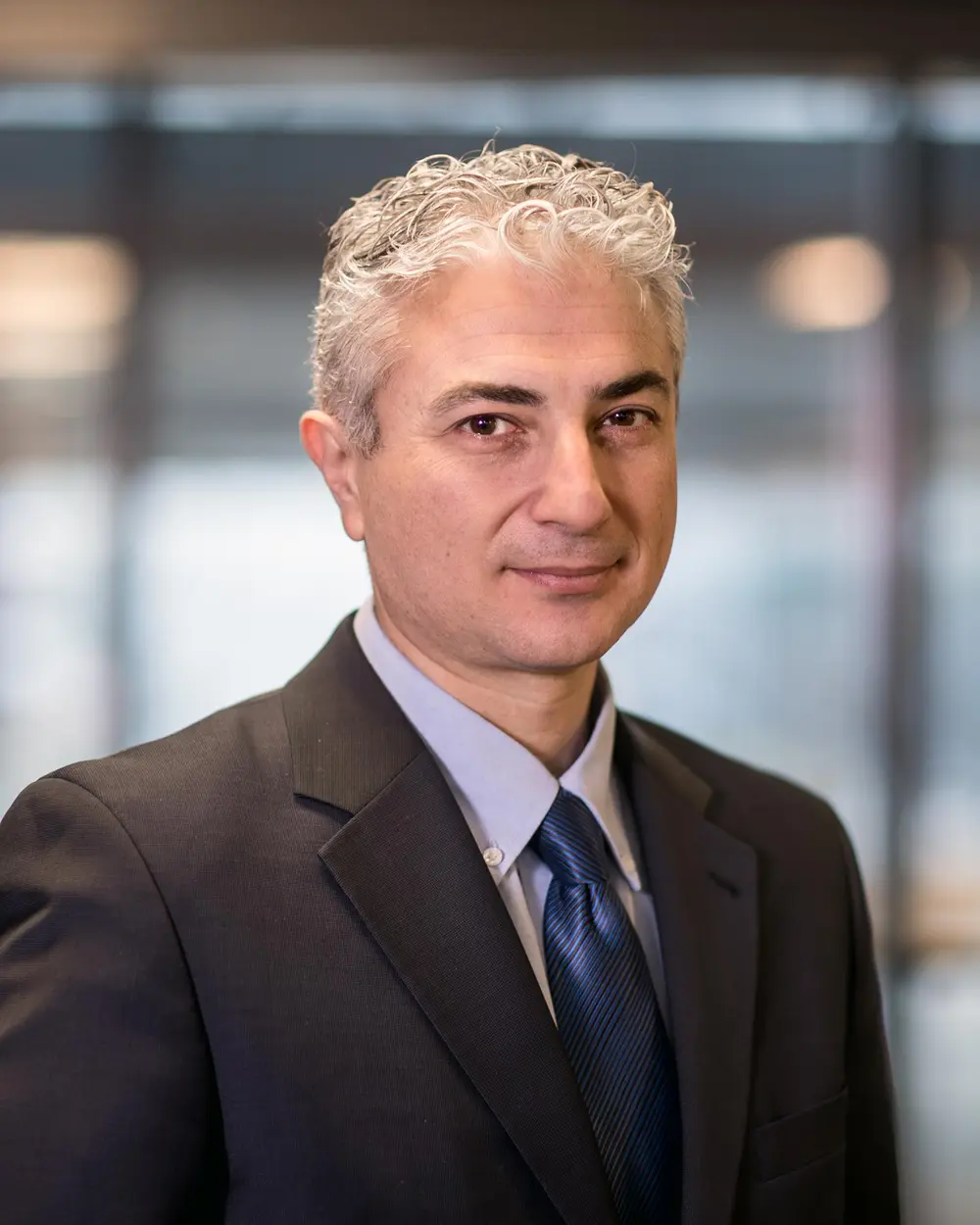