Silicium vervangt grafiet als anodemateriaal
LeydenJar Technologies maakt kleinere, lichtere accu
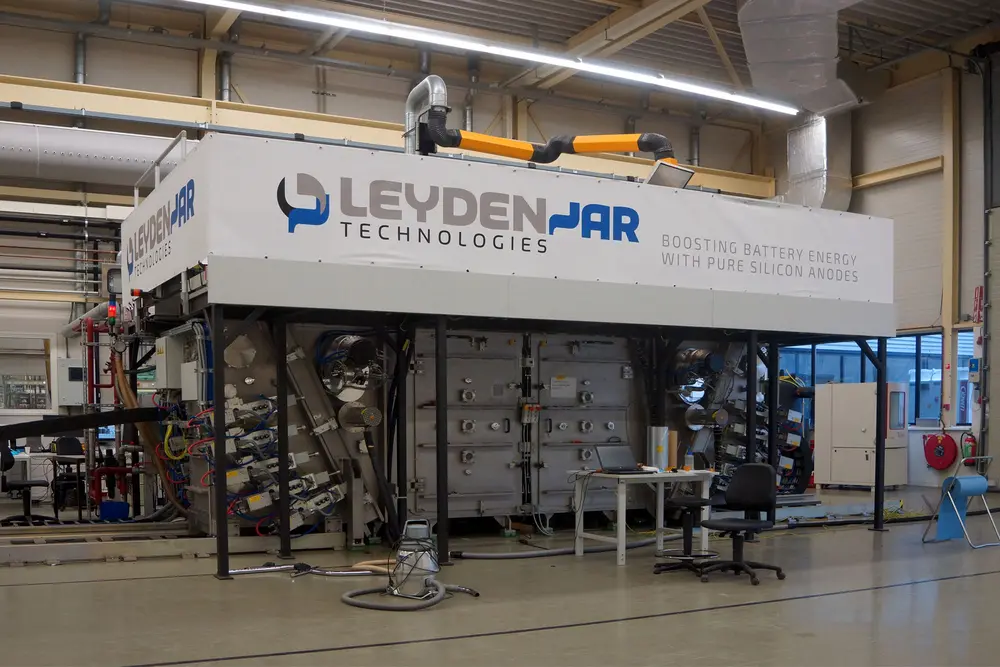
De bottleneck in de ontwikkeling van duurzame elektrische energiesystemen is al langer bekend: de opslag. Weliswaar is de Leidse fles – in principe een eenvoudige condensator – al bijna 275 jaar oud, maar de huidige lithiumcellen zijn nog steeds volumineus en zwaar, en verbruiken schaarse grondstoffen. LeydenJar Technologies heeft er iets op gevonden. Een gesprek met Arjen Didden, R&D Process Technology bij deze Leids-Eindhovense start-up.
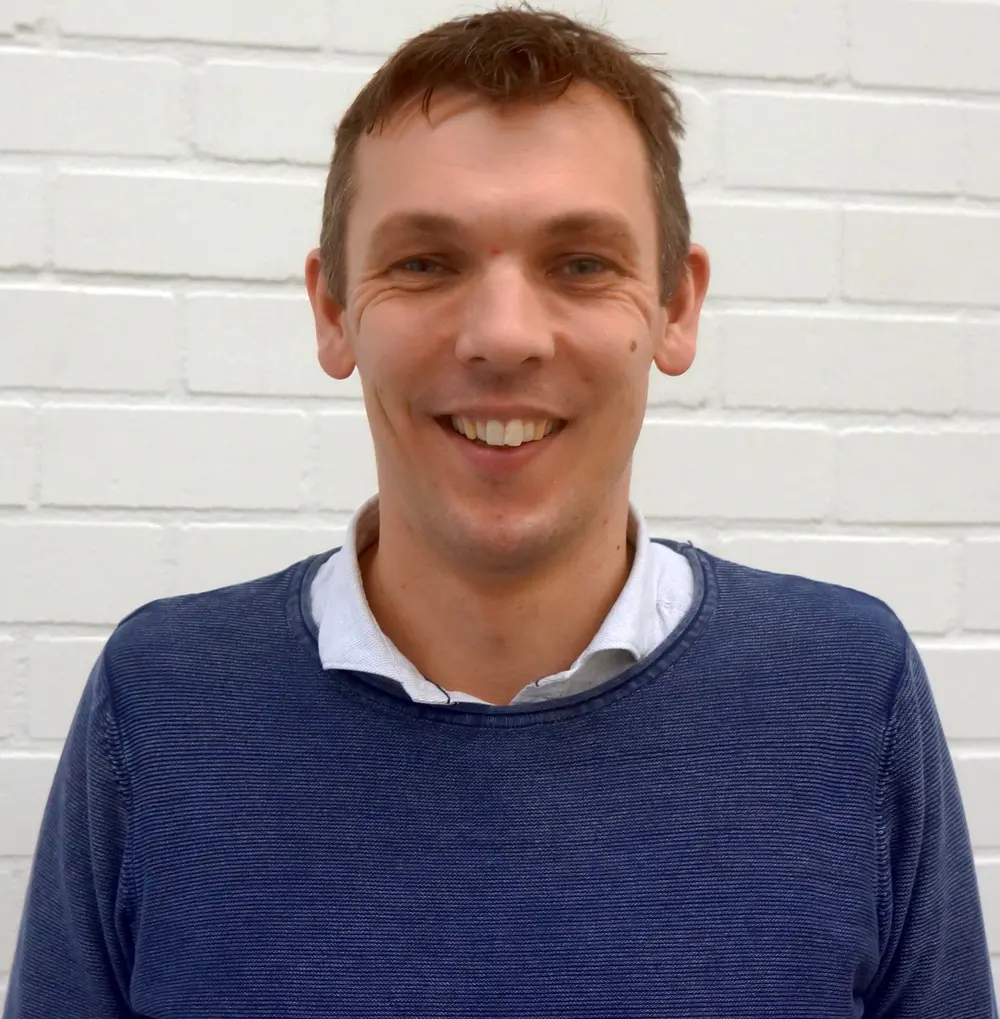
"Het gebruik van silicium in plaats van grafiet betekent een winst in energiedichtheid
van 800 naar 1.000 tot zelfs 1.200 Wh/l"
Productie flexibele zonnecellen
LeydenJar werd in 2016 opgericht door Christian Rood en Gabriel de Scheemaker.
“Zij kwamen uit de financiële hoek en werkten als consultant bij ECN in Petten, waar ze de technologie tegenkwamen” vertelt Arjen Didden. "ECN wilde die graag valoriseren. Het principe was min of meer bij toeval ontdekt, maar paste eigenlijk niet zo goed in de onderzoeksplannen van ECN. Daarop besloten de twee om de ontwikkeling in eigen handen te nemen.”
De machines die in de hal van LeydenJar staan opgesteld zijn eigenlijk ontworpen voor de productie van flexibele zonnecellen. Dat mislukte, onder meer doordat de opgedampte laag silicium (Si) niet het vereiste hoge kwaliteitsniveau had voor efficiënte zonnecellen. Wim Soppe, de bedenker van de technologie, kreeg het idee om de siliciumlaag toe te passen in lithiumbatterijen.
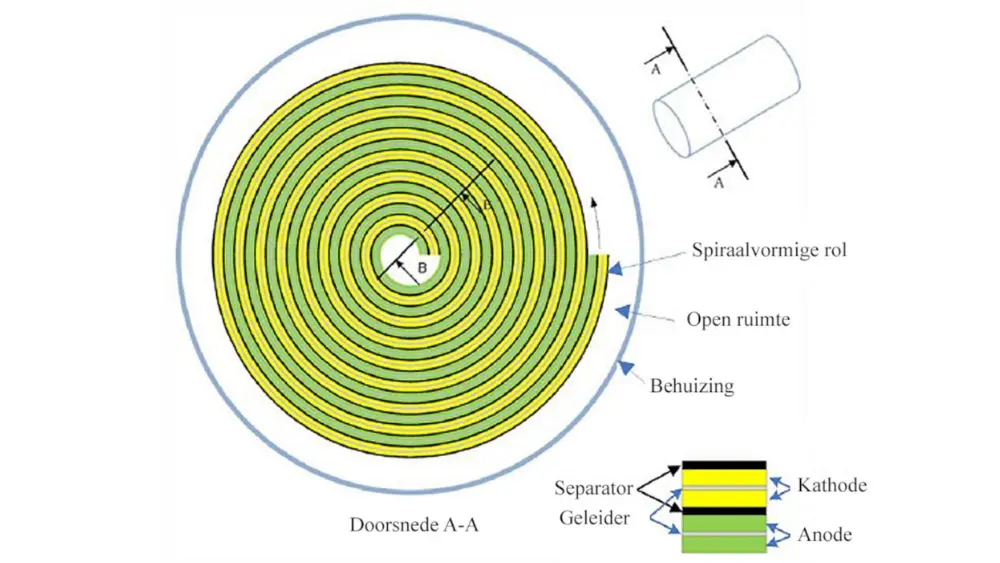
Grafiet of Silicium
Silicium (Si) kwam al van bij het begin van de lithiumtechnologie in de kijker als mogelijk anodemateriaal. “Silicium kan veel meer lithiumatomen opnemen dan grafiet, het traditionele anodemateriaal." aldus Didden. "Het probleem is dat silicium daarbij enorm uitzet, de toename van het volume kan wel 300% bedragen. Daardoor verpulvert het materiaal snel. Bovendien is de geleidbaarheid minder dan die van grafiet en is het materiaal ook vrij moeilijk te hanteren.”
In de huidige accutechnologie wordt aan het grafiet 10 tot 20% Si-poeder toegevoegd voor een hogere energiedichtheid. Maar de grafietlaag op een traditionele anode blijft wel zo’n 80 µm dik - tot 40% van het celvolume.
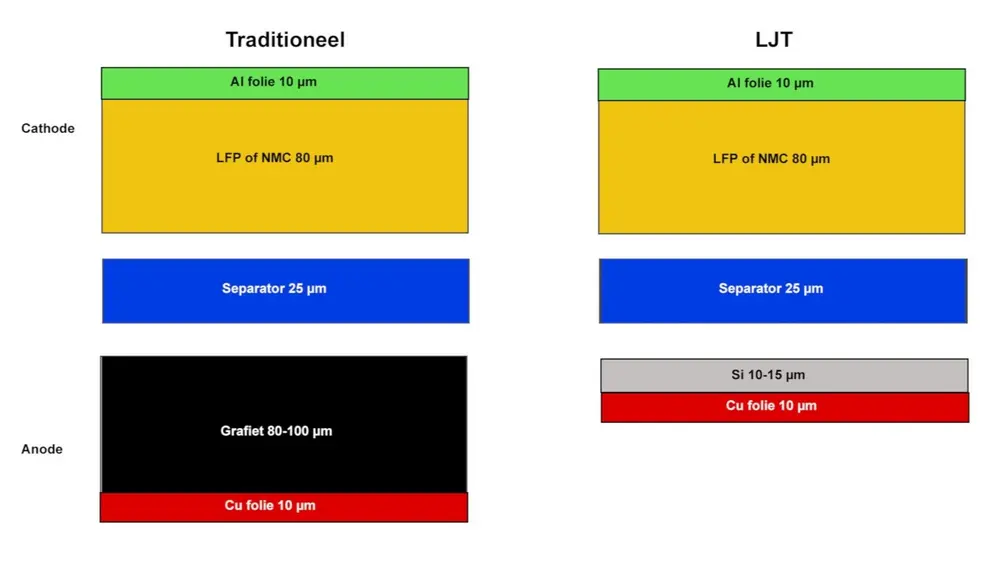
De verschillende laagjes van kathode en anode in een lithiumcel: links de traditionele opbouw, rechts de LeydenJar-oplossing. Het verschil in volume is duidelijk (LFP = Lithium-ijzerfosfaat, LiFePO4; NMC = Nikkel-mangaan-kobaltoxide LiNixMnyCozO2)
Kolommetjes
De bij LeydenJar geproduceerde Si-laag is slechts 10-15 µm dik, en die maat is min of meer stabiel doordat de opbouw columnair is. Dat wil zeggen dat door de depositietechniek de siliciumdeeltjes een soort ‘kolommetjes’ vormen, wat een zodanig poreuze structuur oplevert dat er ruimte is voor de volumetoename tijdens het lithiëren. De afmetingen van de kolommetjes liggen in de grootteorde van enkele honderden Nm tot een µm. “Met silicium is dus een aanzienlijke volumebesparing mogelijk: de energiedichtheid kan oplopen van zo’n 800 naar 1.000-1.200 Wattuur per liter. Dat is waar wij ons op richten. Ook het gewicht van onze cellen is minder – ook al omdat de behuizingen bij een gelijke energie-inhoud kleiner te maken zijn.”
zoektocht naar alternatieve elektrolyten
Er zijn natuurlijk nog allerlei problemen die om een oplossing vragen. Zo is de vorming van SEI (Solid Electrolyte Interphase), een afvalproduct dat ontstaat daar waar de anode in contact komt met de elektrolyt. Dat is een belangrijke factor in het verouderingsproces van Li-cellen, in het bijzonder voor Si-anodes.
“Niet iets dat we kunnen oplossen met onze productietechnologie, maar er wordt wel driftig onderzoek gedaan naar alternatieve elektrolyten,” zegt Didden, “onder meer in ons batterijlab in Leiden, waar er zich twee onderzoekers mee bezighouden, in samenwerking met de TU Delft en de universiteit van Münster (D).
Het probleem heeft een chemische aard. Zowel silicium als lithium reageren sterk met de gebruikelijke oplosmiddelen: (gefluorideerde) carbonaten. Het gevolg is dat er SEI-laagjes om de siliciumkolommen ontstaan die de uitwisseling van ionen verstoren. Stabiele anodes vereisen dus een geschikt elektrolyt.”
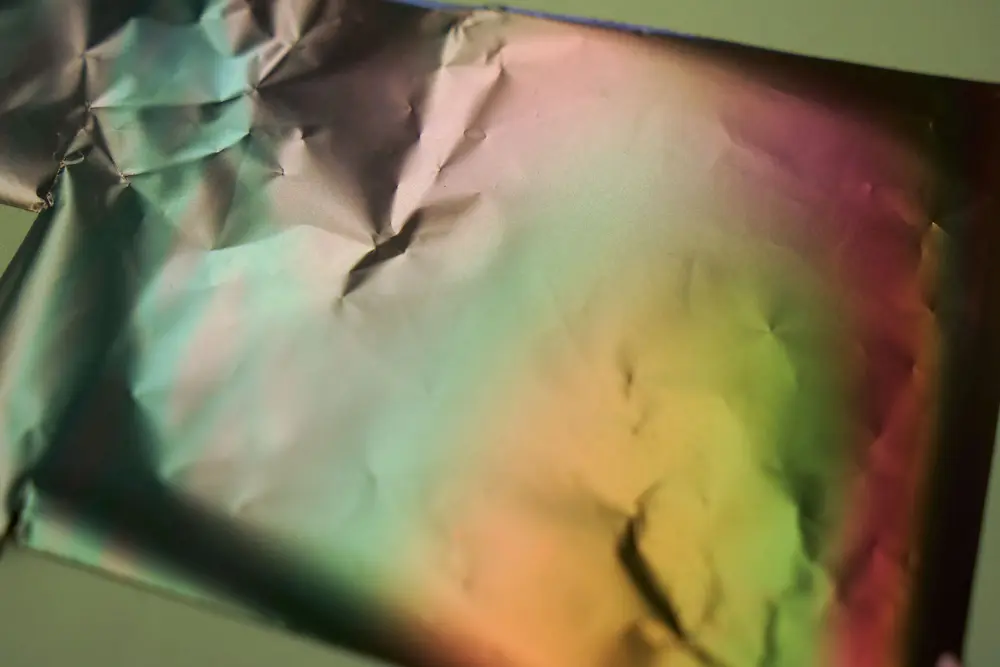
Niet alleen
Voor de perfectionering van de Li-cel houdt LeydenJar contact met de onderzoeksgroep in Delft (Marnix Wagemakers) en ZSW in Ulm (D). “Zij maken met hun batterijproductielijn grotere cellen voor ons. Bepaalde bedrijven gaan zelfs al de richting uit van een commerciële productie met Si-Li-cellen. Het is een enorm hot topic, op het moment.”
Dat geeft wel aan dat er een serieuze businesscase voor de start-up is; de behoefte aan accucapaciteit zal in de komende jaren waarschijnlijk exponentieel stijgen.
“Eens we de problemen met de anode hebben opgelost, dient zich de volgende bottleneck aan: waar halen we de schaarse grondstoffen voor de kathode vandaan, zoals het nikkel en kobalt in NMC-cellen? Als je het al kunt vinden, heeft de winning in vele gevallen nare gevolgen voor milieu en mensenrechten. Er zijn wel oplossingen, zoals de minder kobalt bevattende NMC‑6‑2‑2 of 8‑1‑1 legeringen, maar die moeten nog verder worden uitontwikkeld.”
PECVD
Hoe dan ook, de ontwikkeling lijkt niet te stuiten, en LeydenJar geeft zich een goede kans om daarvan deel uit te maken.
Didden is overtuigd: “Vergeet niet dat ons productieproces een stuk eenvoudiger is dan dat van de traditionele grafietelektrode. Daarvoor moet eerst het mengsel worden gemaakt, met slot-dye coating op het substraat worden aangebracht, vacuümgedroogd en tot slot gekalanderd. Een heel gedoe.”
“Onze coating wordt in één keer aangebracht, door middel van Microwave PECVD (Plasma Enhanced Chemical Vapor Deposition), een techniek waarin de elektromagnetische straling van magnetrons een plasma creëert waarin silaanmoleculen worden gekraakt en amorf silicium neerslaat op het substraat.
De magnetrons gebruiken weliswaar flink wat energie, maar uit de life cycle analysis blijkt dat de carbon footprint van ons proces misschien nog wel kleiner is dan die van het traditionele proces.”
Businessmodel
LeydenJar Technologies heeft momenteel zeven mensen in dienst, en binnenkort worden dat er meer. De start-up is uiteraard niet van plan om met grote bestaande accuproducenten te gaan concurreren. Met de investeringen die ze tot op heden hebben opgehaald – zo’n 4 miljoen van de EU en institutionele en informele beleggers – willen ze de technologie perfectioneren en bewijzen dat ze zonder grote meerkosten, de energiedichtheid van Li-accu’s met ongeveer de helft kunnen vergroten.
“We mikken op de productie van de machines voor de productie van ons anodemateriaal. Daarvoor zullen we onze patenten en recepten goed moeten beschermen – wat niet eenvoudig is in het huidige economische klimaat – maar daarom willen we ons in eerste instantie beperken tot Europa. Daar is ook heel veel activiteit op dit gebied, met name bij Duitse autofabrikanten.”
“Een andere mogelijkheid is dat we ons, als de productiemethode eenmaal is uitontwikkeld, laten overnemen door een accuproducent. Voor de investeerders zou dat ook heel aantrekkelijk kunnen zijn. Het is tenslotte een groot risico om een eigen productiebedrijf op te zetten – al hebben we een buurman (ASML) die bewezen heeft dat dit wel degelijk mogelijk is.”